Improve Mining Equipment Maintenance for Safe Environment
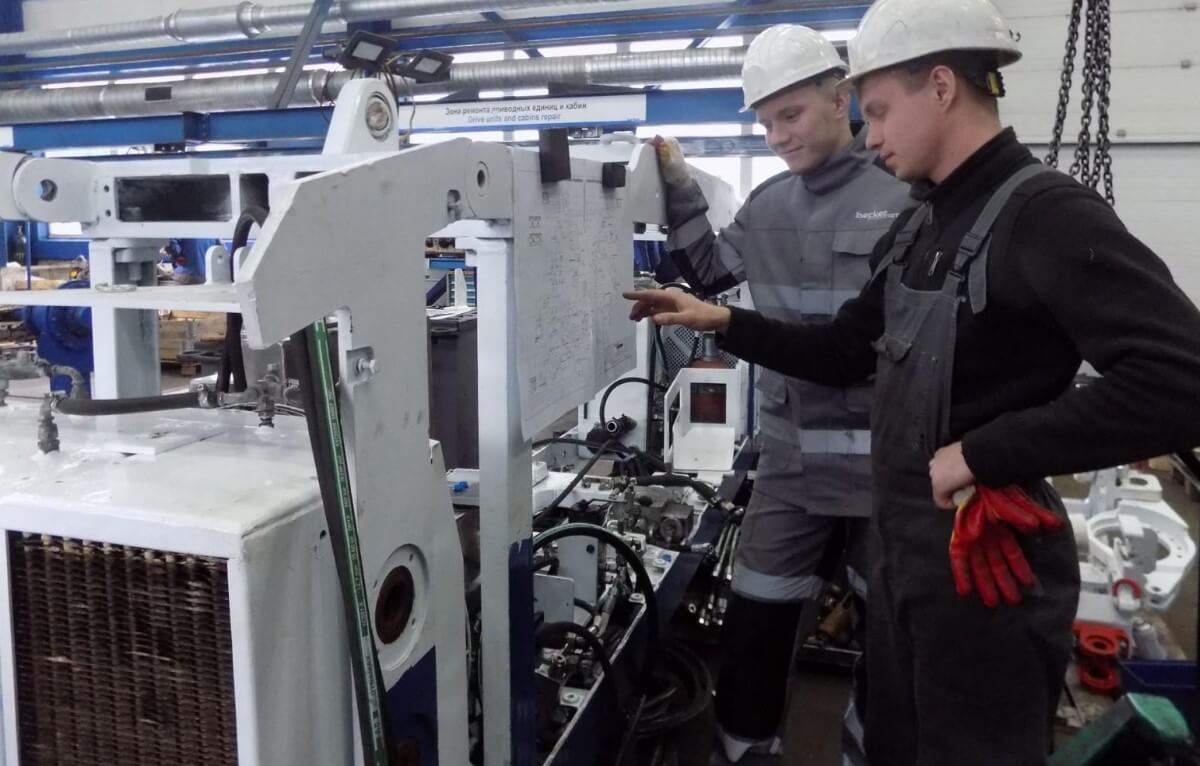
The mining industry, with its history marred by tragic incidents like the Senghenydd Colliery disaster in 1913 and the Monongah mining disaster in 1907, has long been associated with risk and danger. Despite significant technological advancements, accidents involving mining equipment still occur today, underscoring the critical need for robust safety measures and diligent equipment maintenance.
As of 2019, the United States boasted approximately 13,000 active mines, contributing to a thriving industry valued at $61 billion. These mines primarily extract metals, precious metals, and minerals using advanced tools such as explosives, drills, and conveyors. However, even in this modern era, mining accidents claimed the lives of 37 individuals in the US in 2021 alone. This alarming statistic highlights the essential role that equipment maintenance and safety play in mining operations.
GET IN TOUCH
In a hurry? Call us at +1-724-515-4993
Inadequate Mining Equipment Maintenance
Responsible for a substantial 30% of mining injuries. These injuries can result from fires, floods, explosions, poorly designed or maintained equipment, and human error. Therefore, prioritizing maintenance tasks, adhering to safety protocols, and ensuring equipment remains in optimal working condition are paramount for the mining industry’s success and the safety of its workforce.
Becker Mining, a renowned name in the mining sector, emphasizes the importance of thorough equipment cleaning. The inherently dusty and grimy mining environment demands regular and meticulous cleaning of heavy mining equipment using appropriate tools and products. Maintaining clean equipment reduces the likelihood of breakdowns, production halts, and mitigates safety concerns.
Education And Training Of Workers Are Equally Critical.
The mining industry employs highly specialized equipment, necessitating comprehensive training for workers in operating and maintaining these machines. This approach reduces the occurrence of human error and enhances workplace safety. Equally important is the consistent use of safety equipment, improving site visibility, and strict adherence to electrical safety norms.
Proper documentation of safety procedures and the implementation of a well-defined maintenance strategy are vital components of ensuring safety and efficiency in mining operations. A preventive maintenance program, the identification of critical and non-critical equipment, and keeping maintenance tasks up-to-date form the foundation of this strategy.
In the digital age, many mining companies are leveraging software and maintenance schedules to streamline equipment upkeep. These tools provide a systematic approach to tracking, managing, and executing maintenance tasks, significantly reducing the risk of unexpected breakdowns. Even more innovative is the adoption of predictive maintenance schedules. By utilizing data analysis and machine learning algorithms, these systems can predict when equipment is most vulnerable, enabling proactive maintenance. This approach not only minimizes downtime but also optimizes resource utilization, making it increasingly popular among forward-thinking organizations. The adoption of these technologies signifies a shift in maintenance practices from reactive to predictive, emphasizing the industry’s commitment to safety and efficiency.
GET IN TOUCH
In a hurry? Call us at +1-724-515-4993
The Key Aspects Of Improving Mining Equipment Maintenance And Safety:
1. Cleaning and Maintenance
Adequate cleaning and maintenance of mining equipment cannot be emphasized enough. Mining operations take place in harsh environments characterized by dust, dirt, and debris. Failing to clean equipment regularly can lead to the buildup of these materials, which can, in turn, cause overheating, reduced equipment lifespan, and increased risk of accidents. Companies should invest in appropriate cleaning tools, such as pressure washers and industrial-grade cleaning agents, to keep their equipment in top shape.
Additionally, lubrication of moving parts is crucial to prevent wear and tear. Proper lubrication reduces friction, lowers energy consumption, and extends the life of equipment components. It’s essential to follow manufacturer-recommended lubrication schedules and use high-quality lubricants.
2. Training and Education
The mining industry’s specialized equipment demands a highly trained and knowledgeable workforce. Comprehensive training programs should cover not only equipment operation but also safety protocols and emergency response procedures. Regular refresher courses and evaluations can ensure that workers remain proficient in their roles and aware of the latest safety standards.
Furthermore, fostering a culture of safety is essential. Workers should be encouraged to report potential hazards and participate in safety improvement initiatives. Safety awareness campaigns and incentives can motivate employees to prioritize safety in their daily tasks.
3. Safety Equipment and Visibility
Personal protective equipment (PPE) is a cornerstone of mining safety. Miners should be equipped with appropriate PPE, including helmets, gloves, safety glasses, and respiratory protection. Regular inspections of PPE and replacement of damaged items are essential.
Improving site visibility is another critical aspect of safety. Proper lighting, reflective markers, and warning signs can help prevent accidents, especially in dimly lit or underground mining environments. Installing cameras and sensors on equipment can also enhance visibility and aid in monitoring safety conditions.
GET IN TOUCH
In a hurry? Call us at +1-724-515-4993
4. Documentation and Maintenance Strategy
Establishing a robust documentation system is essential for tracking maintenance tasks, safety procedures, and equipment history. Digital maintenance management systems (CMMS) can streamline this process by providing real-time access to maintenance records and schedules.
A well-defined maintenance strategy should include preventive maintenance programs tailored to each piece of equipment. This involves regular inspections, component replacements, and calibration to ensure optimal performance. Identifying critical equipment, which, if it fails, could have severe consequences for safety and production, is crucial. These critical items should receive extra attention and redundancy planning.
5. Predictive Maintenance
Predictive maintenance, driven by data analysis and machine learning, represents the future of equipment maintenance in the mining industry. By continuously monitoring equipment performance, collecting data on factors such as temperature, vibration, and fluid levels, and applying predictive algorithms, mining companies can forecast when equipment is likely to fail. This allows for proactive maintenance, reducing downtime, minimizing safety risks, and optimizing resource allocation.
Conclusion
Maintaining mining equipment is crucial for ensuring the safety of personnel and the efficiency of mining operations. Regular upkeep can prevent accidents, enhance productivity, and extend equipment lifespan. These steps can significantly enhance operational safety and efficiency in an industry where risk is an ever-present companion. By continually improving equipment maintenance and safety practices, the mining industry can work towards reducing accidents and safeguarding its workforce, while also optimizing production and profitability.
Learn More With Us
Contact us today or visit our website to learn more about mining equipment maintenance and safety. We can take you through the best education for your business now.
Products That We Offer
- VHF Leaky Feeder System
- UHF Leaky Feeder System
- SMARTSENSE®FIXED MONITOR
- RNG-500VHF Leaky Feeder Cable
- UHF Low Loss Leaky Feeder Cable
- Kenwood NX-203/303 Radios
Take control of your mining communication systems today! With Becker Wholesale Mine Supply, the leading manufacturer in the USA. Contact us now and revolutionize your mining communication systems!
GET IN TOUCH
Take the first step towards powering up your operations, call us at +1-724-515-4993