How to Streamline Gas Detector Maintenance
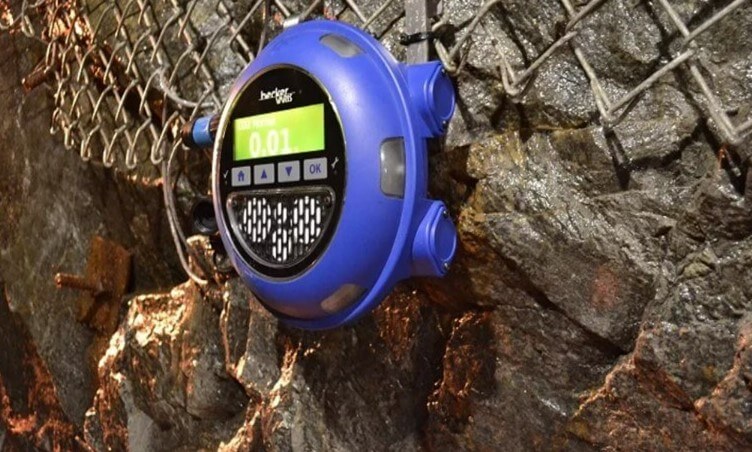
In the industrial and mining sectors, the importance of gas detectors cannot be overstated. These devices play a crucial role in safeguarding workers from the dangers of hazardous gases and ensuring the safety and efficiency of operations. However, maintaining these detectors can be complex and time-consuming. This guide will explore strategies to streamline gas detector maintenance, enhancing both safety and operational efficiency.
Understanding the Importance of Gas Detector Maintenance
Gas detectors are essential for monitoring the presence of harmful gases such as methane, carbon monoxide, hydrogen sulfide, and others. Regular maintenance is critical to ensure that these detectors function accurately and reliably. Proper maintenance helps in:
- Preventing False Alarms: Regular checks and calibrations help avoid false alarms that could disrupt operations and cause unnecessary panic.
- Ensuring Accurate Readings: Accurate gas detection is vital for making informed safety decisions and protecting workers’ health.
- Extending Equipment Life: Routine maintenance can prevent breakdowns and extend the lifespan of gas detectors, saving on replacement costs.
- Compliance with Regulations: Adhering to maintenance schedules helps meet regulatory requirements and avoid potential fines or legal issues.
Key Components of Gas Detector Maintenance
To streamline gas detector maintenance, it’s important to understand the key components and procedures involved. This includes:
- Calibration: Gas detectors must be calibrated regularly to ensure they provide accurate readings. Calibration involves exposing the detector to known concentrations of gas to verify its response.
- Sensor Replacement: Sensors in gas detectors have a limited lifespan and may need to be replaced periodically. Regular checks can help identify when a sensor is nearing the end of its life.
- Battery Checks: Gas detectors rely on batteries for power. Regular battery checks and replacements are necessary to ensure the device remains operational.
- Cleaning: Dust, dirt, and other contaminants can affect the performance of gas detectors. Regular cleaning helps maintain optimal function.
- Testing Alarms: The alarm functions of gas detectors should be tested regularly to ensure they are working correctly and can alert users to gas hazards.
- Documentation: Keeping detailed records of maintenance activities, including calibration dates, sensor replacements, and battery changes, is essential for tracking and auditing purposes.
GET IN TOUCH
In a hurry? Call us at +1-724-515-4993
Streamlining Gas Detector Maintenance
Efficient gas detector maintenance involves several strategies to make the process more manageable and less time-consuming. Here are some practical tips:
1. Implement a Maintenance Schedule
Establishing a clear maintenance schedule is the first step in streamlining gas detector maintenance. A well-organized schedule ensures that all detectors are serviced at regular intervals, reducing the risk of overlooked maintenance tasks. Consider the following steps:
- Determine Frequency: Decide on the frequency of calibration, sensor replacements, and other maintenance tasks based on the manufacturer’s recommendations and operational needs.
- Use a Maintenance Calendar: Create a calendar or use maintenance management software to track upcoming maintenance tasks and deadlines.
- Automate Reminders: Set up automated reminders for maintenance activities to ensure timely completion and avoid missed tasks.
2. Utilize Maintenance Management Software
Investing in maintenance management software can greatly enhance the efficiency of gas detector maintenance. Such software can help with:
- Tracking Maintenance Activities: Maintain detailed records of all maintenance tasks, including calibration dates, sensor replacements, and battery changes.
- Generating Reports: Generate reports to analyze maintenance trends, identify issues, and make informed decisions about equipment management.
- Scheduling and Reminders: Schedule regular maintenance tasks and receive automated reminders to ensure timely completion.
3. Train Personnel
Proper training for personnel involved in gas detector maintenance is crucial for ensuring effective and efficient maintenance practices. Training should cover:
- Maintenance Procedures: Provide detailed instructions on how to perform calibration, sensor replacements, battery checks, and other maintenance tasks.
- Safety Protocols: Ensure personnel are aware of safety protocols when handling gas detectors and performing maintenance tasks.
- Troubleshooting: Train staff to identify and troubleshoot common issues with gas detectors, reducing downtime and improving response times.
4. Standardize Maintenance Procedures
Standardizing maintenance procedures helps ensure consistency and efficiency in gas detector maintenance. Develop standard operating procedures (SOPs) for:
- Calibration: Create a step-by-step guide for calibrating gas detectors, including the required equipment and procedures.
- Sensor Replacement: Develop a procedure for replacing sensors, including guidelines for identifying when sensors need replacement.
- Cleaning: Establish a cleaning protocol to ensure all detectors are regularly cleaned and maintained.
GET IN TOUCH
In a hurry? Call us at +1-724-515-4993
5. Conduct Regular Audits
Regular audits of gas detector maintenance practices can help identify areas for improvement and ensure compliance with maintenance schedules. Audits should include:
- Review of Maintenance Records: Check maintenance records to verify that all tasks have been completed on schedule and that documentation is accurate.
- Inspection of Equipment: Inspect gas detectors to ensure they are in good working condition and that maintenance tasks have been performed correctly.
- Feedback from Personnel: Gather feedback from staff involved in maintenance to identify any challenges or areas for improvement.
6. Adopt Preventive Maintenance Practices
Preventive maintenance practices can help reduce the likelihood of unexpected equipment failures and extend the life of gas detectors. Consider the following:
- Predictive Maintenance: Use data and analytics to predict when maintenance tasks will be needed based on equipment performance and usage patterns.
- Proactive Replacements: Replace components such as sensors and batteries before they reach the end of their useful life to prevent unexpected failures.
7. Optimize Inventory Management
Efficient management of spare parts and maintenance supplies is essential for minimizing downtime and ensuring that maintenance tasks can be performed promptly. Key strategies include:
- Stock Management: Keep an inventory of essential spare parts, including sensors and batteries, to ensure they are readily available when needed.
- Supplier Relationships: Maintain good relationships with suppliers to ensure timely delivery of replacement parts and other maintenance supplies.
- Inventory Tracking: Use inventory management software to track stock levels and avoid shortages.
Conclusion
Streamlining gas detector maintenance is essential for ensuring the reliability and effectiveness of these critical safety devices. By implementing a structured maintenance schedule, utilizing management software, training personnel, standardizing procedures, conducting regular audits, adopting preventive practices, and optimizing inventory management, you can enhance the efficiency of your maintenance processes and safeguard the health and safety of your workforce.
Becker Wholesale Mine Supply is committed to providing high-quality gas detectors and support for effective maintenance practices. For more information on our products and services, or to get expert advice on streamlining your gas detector maintenance, contact us today.
Products That We Offer
- VHF Leaky Feeder System
- UHF Leaky Feeder System
- SMARTSENSE®FIXED MONITOR
- RNG-500VHF Leaky Feeder Cable
- UHF Low Loss Leaky Feeder Cable
- Kenwood NX-203/303 Radios
Take control of your mining communication systems today! With Becker Wholesale Mine Supply, the leading manufacturer in the USA. Contact us now and revolutionize your mining communication systems!