How Does Underground Mining Work
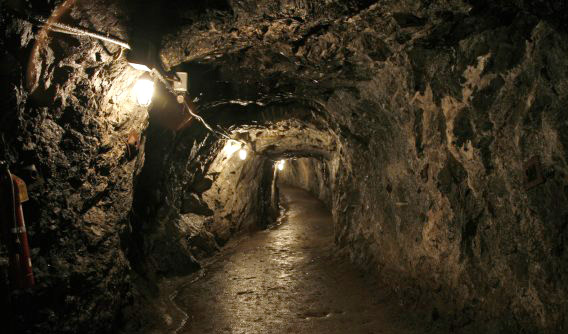
How does underground mining work? Underground mining is a critical process for extracting valuable minerals and resources from the earth. This method of mining involves the excavation of tunnels and shafts, which allow miners to access ore deposits located deep underground. Underground mining can be a dangerous and challenging process, as it requires specialized equipment, techniques, and safety protocols. Despite these challenges, underground mining work remains an essential process for the mining industry and plays a crucial role in the global economy.
Hard-Rock Underground Mining
There are underground mines that are made of hardrock, and underground mines that are made from softrock. For example, coal deposits live in soft sedimentary rocks. The igneous or metamorphic rocks that contain gold deposits are relatively hard.
Although design and extraction methods can vary within hard-rock categories, they all tend to revolve around the same basic principles.
Room and Pillar
For deposits of relatively flat ore, where there is little elevation change, miners drill access ramps to the deposit. They then remove ore using a series of holes (rooms), and roof supports (pillars). You can mine the rooms using traditional charge-and blast techniques or, more often, with a machine known as a continuous miner. The continuous miner digs into the rock to form an excavated area, approximately 20-30 feet (6-9 meters) in length. A rock pillar is then left to support the “roof”. The machine moves through the ore creating rooms and columns until it covers the entire deposit. The machine makes a final pass through the pillars in order to recover any ore. As it leaves each room, the roofs will collapse behind it.
Cut and Fill
Miners drill an access ramp to the ore deposit from the surface to the lowest point. The operator drives a drill through ore to create a drift or horizontal cut from one end of the deposit. For the hardest rocks, there is no need for roof support. However, softer rock bolts can be used to attach the roof to the drill as it progresses. After the drift is completed, the backfill (or waste material) is spread in the drift to create a platform for the next pass. To cut more ore, the drill will drive on top of the backfill. The drill continues this process until it cuts another drift through the ore deposit.
This technique can also be used to extract larger deposits by drilling two adjacent access ramps. Also, you can cut two adjacent drifts.
Cut and fill is best for hard rock because it doesn’t have the support mechanisms that are central to a method such as room and pillar. The room-and pillar approach crosses easily into the soft stuff, and most coal mines.
Soft-Rock Underground Mining
Soft rock is home to coal, salt, uranium and phosphate. There are two main methods of soft-rock mining: room and pillar and longwall. The most common method of extracting coal is the room-and pillar method. Longwall mining is growing in popularity, however.
Longwall Mining
is extremely efficient. Instead of drilling through the ore deposit, a lengthy wall machine cuts across it, cutting slices up to 600 ft (182m) in length. These slices are then dropped onto a conveyor that moves continuously, and it transports them to a haulage shaft which lifts it from the mine. The roof supports in longwall mining are built into the machine. They sit between the roof of the room and the top of a longwall miner. The supports move along with the machine as it enters the ore. This allows the support area to collapse and fill in the excavated space.
The longwall method is capable of recovering up to 90% of the ore available. The room-and pillar method typically recovers around 50 percent.
If the deposit is narrower, it’s possible to make shorter cuts. This is shortwall mining.
Although blast mining is still a popular technique that uses explosives such as TNT to extract ore, it is only 5% of U.S. production.
Mining is now becoming more efficient. Underground mining is less labor-intensive, and therefore puts fewer people at risk as they work below the surface. Underground mines aren’t the most safe.
Dangers in Underground Mining
Underground mining has a significant environmental impact. This includes air pollution, changes to water flow patterns, chemical and natural gas seepage into soil and water supplies, and inaccessible fires from abandoned mines. It can also result in dramatic changes in the land composition that could make the area unusable once the mining is finished.
Accidents are often caused by the collapse of mine props due to earthquakes. Explosions can also cause casualties if ventilation systems fail to remove exhaust from the mining equipment, coal dust, and natural underground gas leaks. Explosions can be ignited by blasting, which can cause death from the explosions and subsequent collapse of mine structures.
Long-term health issues can pose a serious risk to your job. Lung diseases such as pneumoconiosis and the dreaded “black lung” can be caused by inhaling mineral dust. Respiratory diseases can also be caused by breathing in welding fumes or radon, which are often found in mines. It is also common to suffer from hearing loss due to loud equipment or back injuries when lifting heavy loads.
Contact Us
Mining equipment is a critical component of the mining industry, and having the right equipment can mean the difference between success and failure. At Becker Wholesale Mine Supply, we offer a wide range of mining equipment, including radios, leaky feeder systems, gas monitors, and more. Our products are designed to meet the rigorous demands of the mining industry, ensuring that you have the best equipment for the job. Contact us today to learn more about our products and how we can help you get the equipment you need to succeed in the mining industry.