Gas Leak Detection: A Critical Tool for Industrial Safety
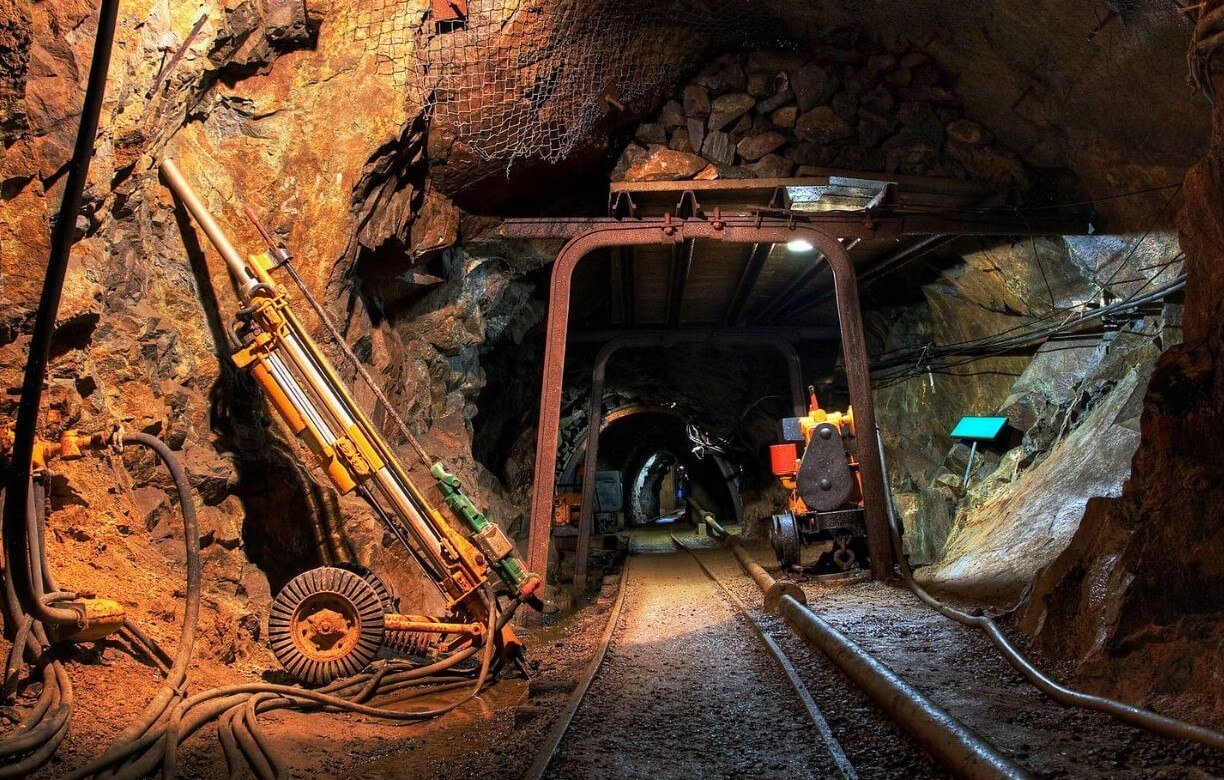
In industrial environments, safety is paramount. One of the most significant threats to worker safety and environmental integrity is the potential for gas leaks. Gas leak detection is a critical component of industrial safety systems, playing a vital role in preventing catastrophic events, ensuring compliance with regulations, and safeguarding both human life and the environment. This blog post delves into the importance of gas leak detection, the technologies available, and best practices for implementation in industrial settings.
What is Gas Leaks
A gas leak occurs when natural gas or other gases escape from the containment system, potentially leading to explosive atmospheres, health hazards, and environmental contamination. Common gases involved in industrial operations include:
- Natural Gas (Methane): Widely used as a fuel source, it is odorless and colorless, making it particularly dangerous without detection systems.
- Propane: Often used in heating and fuel applications, propane leaks can lead to explosive concentrations if undetected.
- Ammonia: Common in refrigeration and cleaning applications, ammonia is toxic and poses significant health risks.
- Hydrogen Sulfide (H2S): This highly toxic gas is often found in oil and gas extraction and can be lethal even in small concentrations.
The Dangers of Gas Leaks
Gas leaks can pose immediate and severe risks to industrial facilities:
- Health Hazards: Exposure to certain gases can lead to acute and chronic health issues, including respiratory problems, neurological damage, and even death.
- Explosions and Fires: Accumulation of flammable gases can create explosive atmospheres. The ignition of these gases can lead to fires, destruction of property, and loss of life.
- Environmental Damage: Gases such as methane and ammonia can cause significant harm to the environment. Methane, for example, is a potent greenhouse gas that contributes to climate change.
- Economic Impact: Industrial accidents can lead to costly downtime, legal liabilities, and increased insurance premiums. Investing in gas leak detection can save companies from these financial burdens.
GET IN TOUCH
In a hurry? Call us at +1-724-515-4993
The Role of Gas Leak Detection in Industrial Safety
Gas leak detection systems are designed to identify the presence of harmful gases and alert personnel before they can cause harm. These systems are integral to a comprehensive safety program in industrial settings, providing real-time monitoring and rapid response capabilities.
- Early Detection: Advanced gas leak detection systems can identify even minute concentrations of gas, allowing for immediate corrective action before levels reach dangerous thresholds.
- Regulatory Compliance: Many industries are subject to stringent safety regulations regarding gas handling and emissions. Implementing effective gas leak detection systems helps companies comply with these regulations and avoid fines.
- Emergency Response: In the event of a gas leak, early detection allows for swift emergency response, minimizing the impact on personnel and the environment.
- Peace of Mind: Knowing that gas leak detection systems are in place helps create a safer work environment, boosting employee morale and trust in management’s commitment to safety.
Types of Gas Leak Detection Technologies
Gas leak detection technologies have evolved significantly, incorporating advanced sensors and monitoring systems. Here are some of the most commonly used types:
1. Point Detectors
Point detectors are localized sensors that monitor specific areas for gas leaks. They are typically mounted on walls or ceilings and can detect various gases. When the concentration of gas exceeds a predetermined threshold, the sensor triggers an alarm.
- Advantages: Cost-effective and easy to install.
- Disadvantages: Limited coverage area, requiring multiple units for larger spaces.
2. Open Path Detectors
Open path detectors use beams of light to monitor the air over a specified distance. When gas leaks into the path of the light beam, it absorbs some of the light, triggering an alarm.
- Advantages: Capable of monitoring large areas and detecting low concentrations of gas.
- Disadvantages: Susceptible to environmental factors such as fog or rain, which can interfere with the light path.
3. Infrared Detectors
Infrared detectors identify gases by measuring the absorption of infrared light at specific wavelengths. They are particularly effective for detecting hydrocarbons, making them suitable for natural gas and propane applications.
- Advantages: Highly sensitive and less affected by environmental changes.
- Disadvantages: Generally more expensive than other detection methods.
4. Ultrasonic Detectors
Ultrasonic detectors listen for the high-frequency sounds produced by gas leaks. They can detect leaks even in noisy environments, making them ideal for industrial settings.
- Advantages: Effective for detecting pressurized gas leaks and not affected by the gas’s concentration.
- Disadvantages: Limited to detecting leaks from pressurized systems.
5. Electronic Nose Systems
These systems utilize an array of sensors to mimic the human sense of smell, identifying various gases by their unique chemical signatures. While still emerging, electronic nose technology holds promise for gas leak detection.
- Advantages: Can detect a wide range of gases and their concentrations.
- Disadvantages: Technology is still developing and may not yet be widely available.
Best Practices for Implementing Gas Leak Detection
To maximize the effectiveness of gas leak detection systems, industrial facilities should adopt best practices for implementation and maintenance:
1. Conduct a Risk Assessment
Before installing gas detection systems, perform a thorough risk assessment to identify areas where gas leaks are most likely to occur. This includes evaluating the types of gases used, the potential sources of leaks, and the consequences of a leak.
2. Choose the Right Technology
Select gas detection technology based on the specific needs of the facility. Consider factors such as the types of gases present, the layout of the facility, and the environmental conditions that may affect detection.
3. Regular Maintenance and Calibration
Regular maintenance and calibration of gas detection systems are essential to ensure accurate readings. Create a schedule for routine checks and calibrations, and keep records of maintenance activities.
4. Training and Education
Train employees on the importance of gas leak detection and how to respond in the event of a leak. Conduct regular drills to ensure that everyone knows their roles and responsibilities during an emergency.
5. Integrate with Safety Systems
Integrate gas leak detection systems with other safety systems, such as fire alarms and emergency shutdown systems. This creates a comprehensive safety network that enhances overall safety in the facility.
6. Monitor and Analyze Data
Implement a monitoring system that collects data from gas detection sensors. Analyzing this data can help identify trends, potential issues, and areas for improvement in safety protocols.
GET IN TOUCH
In a hurry? Call us at +1-724-515-4993
The Future of Gas Leak Detection
As technology continues to advance, the future of gas leak detection looks promising. Emerging technologies, such as machine learning and the Internet of Things (IoT), are being integrated into gas detection systems, allowing for even more sophisticated monitoring and analysis.
1. Smart Sensors
Smart sensors can provide real-time data to facility managers, enabling quick decision-making and response. These sensors can communicate with other systems to automate safety protocols, such as shutting down equipment in the event of a gas leak.
2. Predictive Analytics
Using data analytics, companies can predict potential gas leak occurrences based on historical data and patterns. This proactive approach allows for preventative measures to be taken before issues arise.
3. Wireless Technology
Wireless gas detection systems eliminate the need for extensive wiring, making installation easier and more flexible. These systems can be deployed in hard-to-reach areas and can be easily relocated as needed.
Conclusion
Gas leak detection is a critical tool for industrial safety, protecting workers, the environment, and company assets. By understanding the dangers of gas leaks and implementing effective detection systems, industries can create safer work environments and minimize risks. Investing in the right technologies, adhering to best practices, and staying informed about advancements in gas detection will ensure that facilities remain at the forefront of safety and compliance.
At Becker Wholesale Mine Supply, we are committed to providing high-quality gas leak detection solutions tailored to the specific needs of our clients. Our products are designed to enhance safety and reliability in industrial operations, making them an essential investment for any facility. Embrace the power of gas leak detection to safeguard your operations and promote a culture of safety within your organization.
Products That We Offer
- VHF Leaky Feeder System
- UHF Leaky Feeder System
- SMARTSENSE®FIXED MONITOR
- RNG-500VHF Leaky Feeder Cable
- UHF Low Loss Leaky Feeder Cable
- Kenwood NX-203/303 Radios
Take control of your mining communication systems today! With Becker Wholesale Mine Supply, the leading manufacturer in the USA. Contact us now and revolutionize your mining communication systems!