In the mining industry, safety is more than a regulatory requirement—it is a daily commitment to protecting the lives of workers and ensuring smooth operations. Among the most dangerous hazards in mining is the risk of toxic or combustible gas leaks. Gases such as methane, carbon monoxide, and hydrogen sulfide can accumulate quickly in underground environments, often without immediate detection by human senses. This is where the role of a gas leak detector in mining becomes indispensable.
Gas Leak Detector in Mining: Predictive Care
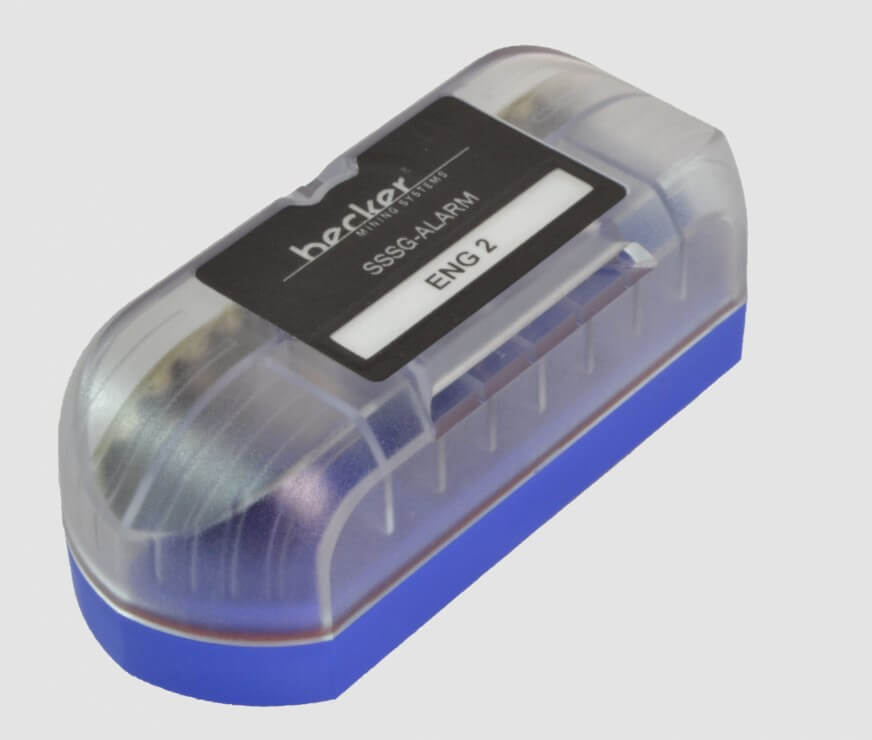